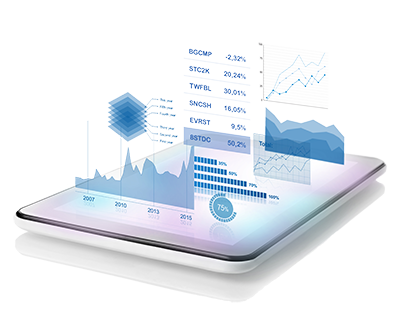
"The definition of vehicle quality has evolved. Vehicle owners now expect defect-free vehicles that are also designed to meet their expectations."
Deliver on expectations
With industry experts and proven methods that yield measurable improvements, we help develop a competitive advantage by integrating the Voice of the Customer into the areas of strategic planning, product development, manufacturing, engineering, supply chain operations, launch and production, and sales and service. Learn more about J.D. Power's solutions >
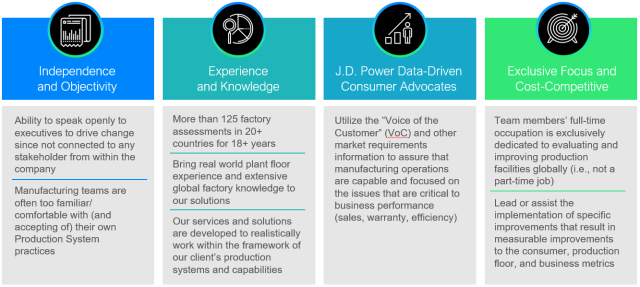
Advisory Consulting Solutions
Client Case Studies
-
US
Improved in-plant detection of powertrain and functional concerns by 27.1 concerns/1000 vehicles resulting in warranty avoidance of over 5,300 claims annually. 30% improvement in 0-MIS warranty & 40% improvement in 1-MIS warranty over 7 months
Improved First Time Capability in Canadian plant by 11% in 6 months
Production System improvements drove a US IQS defect / malfunction performance improvement by 20% over a 3 year period
US OEMs -
Germany
Production System enhancements led to a corporate defect/malfunction improvement of 45% over an 8 year period. Plant awards in 2014 & 2015
QOS Enhancements contributed to a greater than 50% reduction in defect/malfunction problems and a plant award
German OEMs -
Japan
Production System Enhancements contributed to 31% EOL Inspection defect reduction and Plant award for 2 consecutive years
Conducted 2-year on site activities to improve production performance and problem resolution effectiveness resulting in IQS improvement of 20+% over a two year period
Japanese OEMs -
Korea
System Improvements led the way for factory First Time Through improvement of
14% in one year63% reduction in end-of-line defects (as measured by EOL defects per vehicle)
2 year Launch Readiness project led to greenfield plant’s 1st Quartile performance
in first US IQSKorean OEMs -
China
First Time Through improved by over 17% in a 6 month period
End-of-Line DPU improvement of 38% in 9 months
Chinese OEMs -
Suppliers
Improved OEM Customer Reject PPM by 68% over a 6 month period
Supplier modified entire assembly process based on J.D. Power’s launch readiness recommendations
Structural chassis component manufacturer went from being the lowest ranked by
an OEM to above average rank in one yearTier 1 Suppliers